Bag Filters
Bag filters are devices that use fabric bags to filter dust and particulate matter from flue gas streams. They are suitable for various industrial processes that generate high volumes of dust, such as cement production, power generation, waste incineration and metallurgy. Bag filters can achieve high filtration efficiency and low pressure drop, resulting in lower energy consumption and operating costs.
Bag filters are a versatile and critical component in numerous industries, playing a pivotal role in ensuring clean air and process efficiency. These fabric-based filters are adept at capturing fine particulates from gas streams, making them indispensable in sectors where dust and emissions control is paramount.
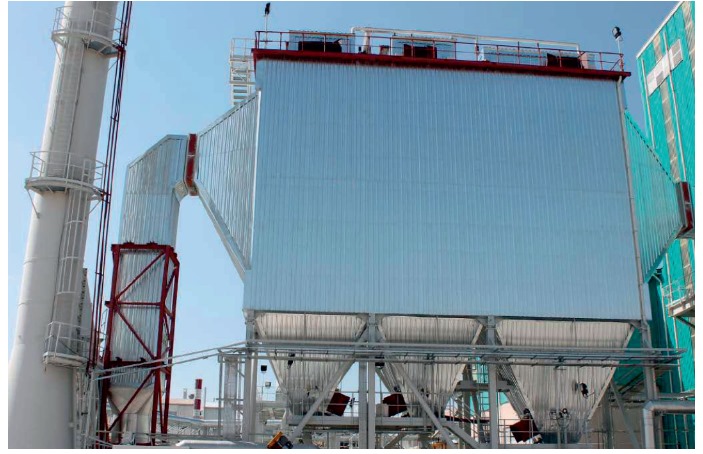
Broad Applications of Bag Filters:
- Cement Production: In cement plants, bag filters remove dust generated during the grinding, mixing, and kiln operations, contributing to product quality and workplace safety.
- Power Generation: They are used to capture fly ash and other combustion byproducts in coal-fired power plants, aiding in compliance with environmental regulations.
- Waste Incineration: Bag filters are employed to filter hazardous emissions from the incineration of medical, municipal, and industrial waste.
- Metallurgy: In iron casting and steel production, bag filters control emissions from furnaces and foundries, capturing metal oxides and other particulates.
- Chemical Industry: They are crucial in chemical manufacturing, where they separate product from waste and control emissions of fine powders and reactive substances.
- Food and Beverage: Bag filters ensure hygiene and quality by removing contaminants from ingredients and finished products in food processing applications.
- Pharmaceuticals: In pharmaceutical production, they maintain cleanroom conditions by filtering out particulates that could contaminate medicines.
- Mining: These filters are used to control dust from mining operations, protecting equipment and improving air quality for workers.
- Water Treatment: They assist in purifying water by removing sediment, sand, and other particles, ensuring clean and safe drinking water.
Advantages Across Industries:
- High Filtration Efficiency: Bag filters can achieve up to 99% efficiency, capturing even sub-micron particulates, which is essential for industries with stringent emission standards.
- Energy Efficiency: With low pressure drops, bag filters contribute to lower energy consumption, reducing operational costs across various applications.
- Customizability: The materials and designs of bag filters can be tailored to specific industrial needs, accommodating a range of temperatures, pressures, and chemical environments.
Maintenance and Considerations:
- Regular Maintenance: To maintain their high efficiency, bag filters require periodic inspection and replacement of bags, which can be a consideration for operational downtime.
- Material Selection: The choice of fabric material is crucial for performance and longevity, as it must resist abrasion, temperature, and chemical exposure specific to each industry.
Specifications
-
Micron rating 1 to 1600 microns
-
Size Varies
-
Flow rate High flow/low pressure drop media
-
Filtration type Surface filtration
-
Chemical compatibility High chemical compatibility
-
Construction Sewn or welded construction with handles and flanges
-
Temp resistance Up to 150°C for polypropylene felt, up to 260°C for polyester felt
Start your free consultation
Let’s assess your needs, analyse your current proccesses and see how Cybertig can implement the change that your organisation requires. We’re here to help.
The Flue Gas & Incineration Blog
In this blog, you will discover how flue gas cleaning systems and hazardous waste/medical incinerators can help you reduce emissions, save costs, and comply with environmental standards. You will also learn about the latest innovations and best practices in the field of energy from waste.
Flue Gas Cleaning: Comprehensive Guide to Technologies, Solutions, and Future Trends
Flue Gas Cleaning: Comprehensive Guide to Technologies, Solutions, and Future Trends Flue Gas Treatment: Ensuring Cleaner Air and Sustainable Operations...
Electrostatic vs. Bag Filters in Cement Industry
Add Your Heading Text Here Electrostatic vs. Bag Filters in the Cement Industry The Basics of Flue Gas Treatment Flue...
2024: Medical Incineration Overview
2024: Medical Incineration Overview What is a medical incinerator? A medical waste incinerator is a device that uses high-temperature combustion...