Cyclones
Cyclones are devices that use centrifugal force to separate dust and particulate matter from flue gas streams. They are often used as pre-filters or co-filters in flue gas cleaning systems to reduce the load on downstream equipment such as bag filters or scrubbers. Cyclones can handle high temperatures and abrasive materials, and have low maintenance and operating costs.
Multicyclones are an integral part of industrial processes where the separation of particulate matter from flue gases is essential. These systems are designed to operate on the principle of centrifugal separation, utilizing multiple cyclone collectors in parallel to enhance efficiency and capacity. The versatility of multicyclones makes them suitable for a wide range of industries, including cement and chemical production, where they play a crucial role in pollution control and product recovery.
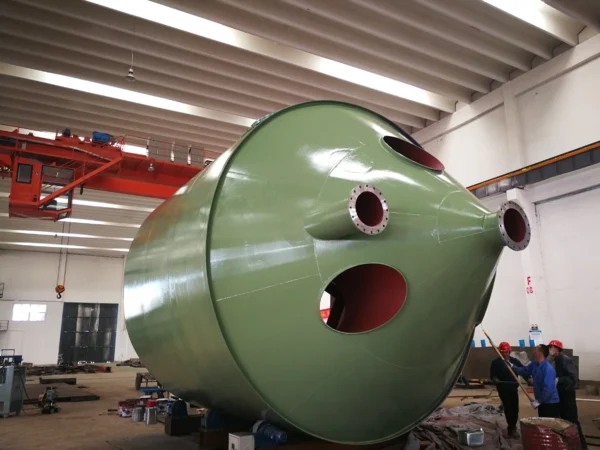
In the Cement Industry:
Multicyclones are employed in cement plants primarily to remove particulate matter from the exhaust gases generated during the clinker production process. The high temperatures and abrasive nature of the particles in cement manufacturing necessitate robust and efficient dust collection systems. Multicyclones, with their ability to withstand harsh conditions and effectively separate coarse particles, are a common choice for pre-cleaning stages before further treatment by fabric filters or electrostatic precipitators.
In the Chemical Industry:
In the chemical process industries (CPI), multicyclones are used to remove solids from streams of air or other gases. This separation is often motivated by the need to reduce environmental impact, recover products, and protect equipment from the wear and tear caused by particulate matter. Multicyclones in the CPI are designed to handle a variety of conditions, including high-temperature gases and corrosive materials. They are valued for their simplicity, lack of moving parts, and relatively low capital and maintenance costs compared to other gas-solid separation methods.
Advantages of Multicyclones:
- High Efficiency: Multicyclones can achieve high collection efficiencies, especially for larger particles. Their design allows for multiple small cyclones to operate in parallel, increasing the overall surface area for particle separation.
- Durability: They can endure extreme temperatures and abrasive particles, making them suitable for industries like cement production.
- Low Maintenance: With no moving parts, multicyclones require less maintenance than other types of dust collectors.
- Versatility: They can be used across various industries and can be tailored to specific process requirements.
Challenges and Considerations:
- Particle Size Limitations: While multicyclones are effective for larger particles, they may have lower collection efficiencies for fine particulates. In such cases, they are often used in conjunction with other dust collection systems.
- Pressure Drop: The design of multicyclones can result in a significant pressure drop, which may lead to higher energy costs for the system.
- Space Requirements: The installation of multicyclones requires careful consideration of space, as they can be larger than single cyclone systems.
In conclusion, multicyclones are a critical component in the arsenal of air pollution control technologies. Their application in industries such as cement and chemical manufacturing underscores their importance in achieving environmental compliance and operational efficiency. As industries continue to seek sustainable and cost-effective solutions, the role of multicyclones in pollution treatment and resource recovery is likely to remain significant
Specifications
-
Inlet velocity 10 to 30 m/s
-
Cut-off size 5 to 50 microns
-
Collection efficiency 70 to 90%
-
Pressure drop 500 to 1500 Pa
-
Material Carbon steel or stainless steel
-
Shape Conical or cylindrical
-
Outlet type Tangential or axial
Start your free consultation
Let’s assess your needs, analyse your current proccesses and see how Cybertig can implement the change that your organisation requires. We’re here to help.
The Flue Gas & Incineration Blog
In this blog, you will discover how flue gas cleaning systems and hazardous waste/medical incinerators can help you reduce emissions, save costs, and comply with environmental standards. You will also learn about the latest innovations and best practices in the field of energy from waste.
Flue Gas Cleaning: Comprehensive Guide to Technologies, Solutions, and Future Trends
Flue Gas Cleaning: Comprehensive Guide to Technologies, Solutions, and Future Trends Flue Gas Treatment: Ensuring Cleaner Air and Sustainable Operations...
Electrostatic vs. Bag Filters in Cement Industry
Add Your Heading Text Here Electrostatic vs. Bag Filters in the Cement Industry The Basics of Flue Gas Treatment Flue...
2024: Medical Incineration Overview
2024: Medical Incineration Overview What is a medical incinerator? A medical waste incinerator is a device that uses high-temperature combustion...